

Senior Design
External Female Catheter Improvement
The core function of this project was to gain realistic experience in the Medical Product Development Process. This entry specifies my contributions and experience within a team effort,
to implement a customer-focused development process specific to the unique requirements surrounding the improvements of external female female catheters.
Specifically my individual efforts toward verification tests.

The existing device:
Bard Purewick Female External Catheter
Verification Testing -
Testing design outputs against acceptance criteria
In this phase of the Medical Product Development Process my team and I generated verification protocols in accordance with FDA guidance regarding medical development based on our verification plan. The team split up the various aspects of design outputs for verification protocol generation and actual testing. I was assigned to the the leakage protocol with my teammate Dammy Ayoola. Together we revised the protocol according to the SOP for document revision and performed the necessary testing, and along the way we identified the potential need for an Engineering Change Order (ECO). We also wrote a report on our testing, and assessed the data against our identified acceptance criteria.
The acceptance criteria were met according to our testing. The testing will be further described below.
​
Our New Device:
Modified Female External Catheter
Revision -
Improving the protocol in order to get reliable results
Early in the verification process Dammy and I identified the need to overhaul the practical considerations, required resources, and steps to perform our verification test. We initially assumed a need to perform testing in the University of Pittsburgh Victoria Hall Nursing Simulation lab. We were able to identify and relocate resources to the Bioengineering Makerspace in Benedum hall to improve resource access and time access to the testing resources.
Upon moving to Benedum we further identified problematic mistakes or lack specification for the test to be performed. We spent time understanding the system better in order to revise the protocol, and implemented the revisions. This process caused us to consider with the team a need to perform an Engineering Change Order. This consideration was undergone before we finalized our revision; therefore our testing was also done after this.

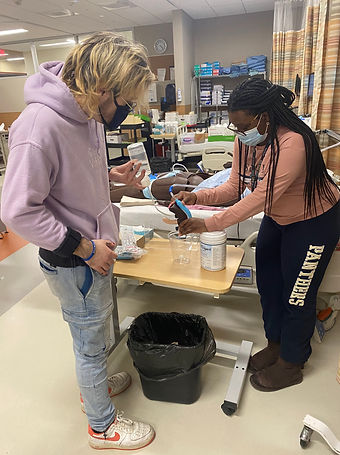
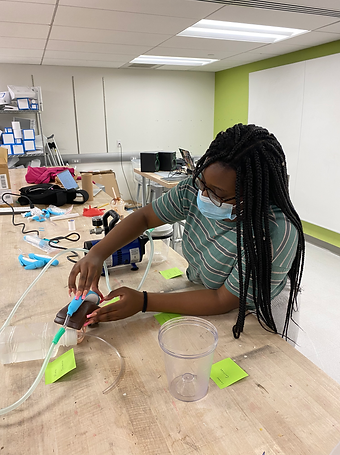
The images above show the process of identifying the practical limitations that required Dammy and I to revise the protocol for Leakage Verification testing (above), as well as a broad scope of the functional components required for our testing (left)
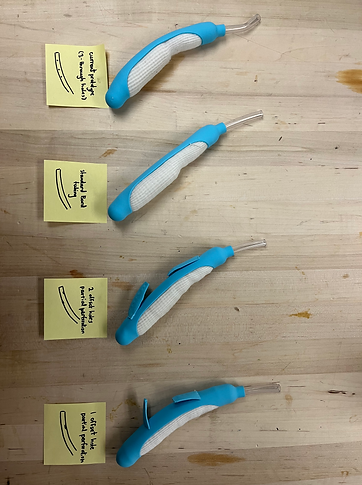

ECO Considerations-
Tubing perforation in our new design proposed potential issue to leakage testing.
The team decided to assess the need for an Engineering Change Order due to issues with leakage testing identified by Dammy and I during our Leakage test protocol revision. This included an assessment of different tubing perforations and was intended to inform any decisions associated with changing the devices specifications.
We approached the assessment with several alternative perforation pattern ideas to identify the prime pattern to ensure that suction would be efficient enough to eliminate excessive leakage. The patterns are identified in the image on the left.
Ultimately, the team decided not to pursue a complete ECO due to the identification that an increase in vacuum pump pressure reduced the leakage to nearly zero mL in our testing.
This assessment was performed by myself and my teammates Matt Kart, Emily Hearty, and Emily Molitoris. The process did result in a change to the intended pump pressure to be used for our device, but did not require any changes to the actual catheter device.
ECO Considerations:
The alternative perforation patterns (top) and the pump used to generate the pressure in our testing (bottom)
Verification Results -
Leakage verification tests using the revised protocols
Dammy and I performed all post-revision formal leakage verification testing in the University of Pittsburgh's Bioengineering Makerspace. The skills lab from Victoria Hall lent us a perineal simulation model that we used for the simulation of urine output from a female urethra. Our testing with the modified device met the acceptance criteria.
​
My primary responsibility in the leakage verification test included: testing setup, data recording, liquid input preparation, visual documentation of testing setup, and the application of the "urine output" into the test models of the modified catheter.
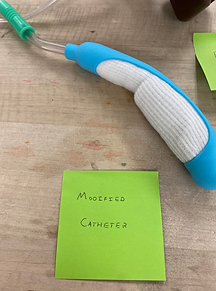

A test model of the modified catheter used for Leakage testing (top), the excerpted datasheet from the report for the leakage test (bottom)

The Senior Design Poster for our Spring Expo Presentation (above) and the final SLA print of the modified catheter I modelled, prior to painting it for the Design Expo (below).

Design -
Design Expo and Final Prototype (Demonstrative)
In preparation for the Design Expo, I was tasked with preparing the final prototype for demonstration. I completed a brand new CAD model of our system under the specifications from our PDS and was able to have it printed and assembled. The team was awarded first place by the judges at Design Expo in the Bioengineering category.
​
The final prototype CAD file was difficult to make. The curvature dimensionality and intent for human form complementation was hard to capture. The process to generate the file took a large portion of the semester and was part of an iterative file generation until the final form was captured.
​
The final form was never intended to be actually tested on, and was always intended to be a demonstrative object. While we did not test this final form, the functional aspects were tested on similarly modified catheters.
​
​
Gantt Chart -
Scheduling Development Efforts
The team ultimately utilized a Gantt chart to record and plan the process of our device's development. From our verification and validation efforts to our FDA documentation considerations and the Design Expo the Gantt neatly shows the process as it developed through the Spring term semester.
​
The Gantt also includes a record of assigned team members for each step in our process, and a preliminary outline of our Spring term schedule. I was ultimately responsible for generation of the Gannt. This required in depth reference to all efforts throughout the semester, deadline implementation and assignment of responsibility based on direction from team division of efforts.
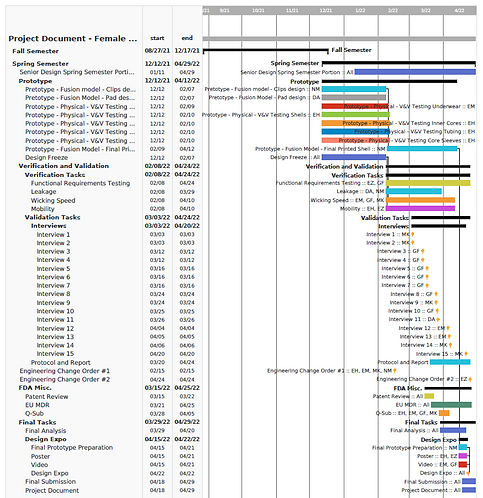
Gantt Chart for the Spring Semester
Spring Semester Summary
The improvements of the female external catheter proposed last semester have been verified and validated. In addition, FDA considerations of Quality Systems, EU MDR documentation, and a Q-submission were completed.
​
The process of verification is the primary focus of this portfolio entry, while the design considerations and efforts are secondarily included to contextualize the importance of the verification for ourl newly modified female external catheter
​
​The efforts of my design team have been extraordinary this semester and our successful development throughout this process have rewarded us with our Design Expo award and successful verification and validation tests through our work this Spring semester.
​
